Finding scalable manufacturing solutions for metal components can be a complex task that requires careful consideration of your specific needs and operational capabilities. As businesses evolve, the demand for precision metal components increases, requiring manufacturers to adopt innovative practices that enhance production efficiency and product quality. This article aims to guide you through the process of identifying and implementing scalable solutions that will enable your metal manufacturing operations to grow sustainably and meet market demands.
Understanding Your Production Requirements
Before delving into scalable manufacturing solutions, it is vital to understand your unique production requirements. Every project may necessitate a distinct set of materials, processes, and tolerances. Analyzing your components’ specifications, such as size, weight, complexity, and material type, provides a clearer picture of your manufacturing needs.
Establishing projected production volumes is essential. Knowing how many units you require will influence the type of manufacturing process you should pursue. If your operations demand large quantities of specific metal components, you might look into methods such as CNC machining or sheet metal fabrication, which are both highly efficient for mass production. Conversely, if lower volumes are needed, processes such as additive manufacturing or custom machining may be more appropriate, providing flexibility without compromising on quality. By absorbing such details about production needs, you can navigate available manufacturing options more decisively.
Evaluating Technology and Automation
In today’s manufacturing landscape, technology and automation play pivotal roles in achieving scalability. The incorporation of advanced technologies like robotics, IoT, and AI can significantly enhance the efficiency of production processes. Automated systems, such as robotic arms and CNC machines, are crucial for maintaining precision while reducing downtime between production runs.
Utilizing IoT devices allows for real-time monitoring of manufacturing processes, enabling immediate adjustments to maintain optimal performance. For your metal component production, integrating these technologies can streamline operations and increase output. A well-planned automation strategy ensures that your manufacturing facility is primed for scaling your production efforts while maintaining top quality. This step is essential for companies looking to expand into competitive markets.
Choosing the Right Materials
Materials selection is another critical component in creating scalable manufacturing solutions. The quality and type of metals used directly affect the strength, durability, and functionality of the parts produced. Consider factors such as cost, availability, and performance characteristics when selecting materials. Common metals used in manufacturing include aluminum, steel, titanium, and brass, each offering distinctive advantages depending on the application.
You should assess how these materials respond to various manufacturing processes. Some metals may be better suited for casting than forging or machining. It may be beneficial to work closely with material suppliers who can provide insights into the availability of materials and emerging options, allowing you to stay ahead in terms of quality and cost-effectiveness. Collaborating with suppliers can also unveil innovative materials that might fit well with IP 68 rated components. This goes especially for applications requiring specific protection against environmental factors.
Implementing Quality Control Procedures
Quality control (QC) is indispensable in achieving scalable manufacturing solutions. Establishing robust QC measures ensures that every component you produce meets stringent industry standards and client expectations. The implementation of a thorough Quality Management System (QMS) can facilitate the adherence to quality benchmarks throughout every stage of the manufacturing process. It’s also vital to invest in proper training for your staff concerning these QC measures.
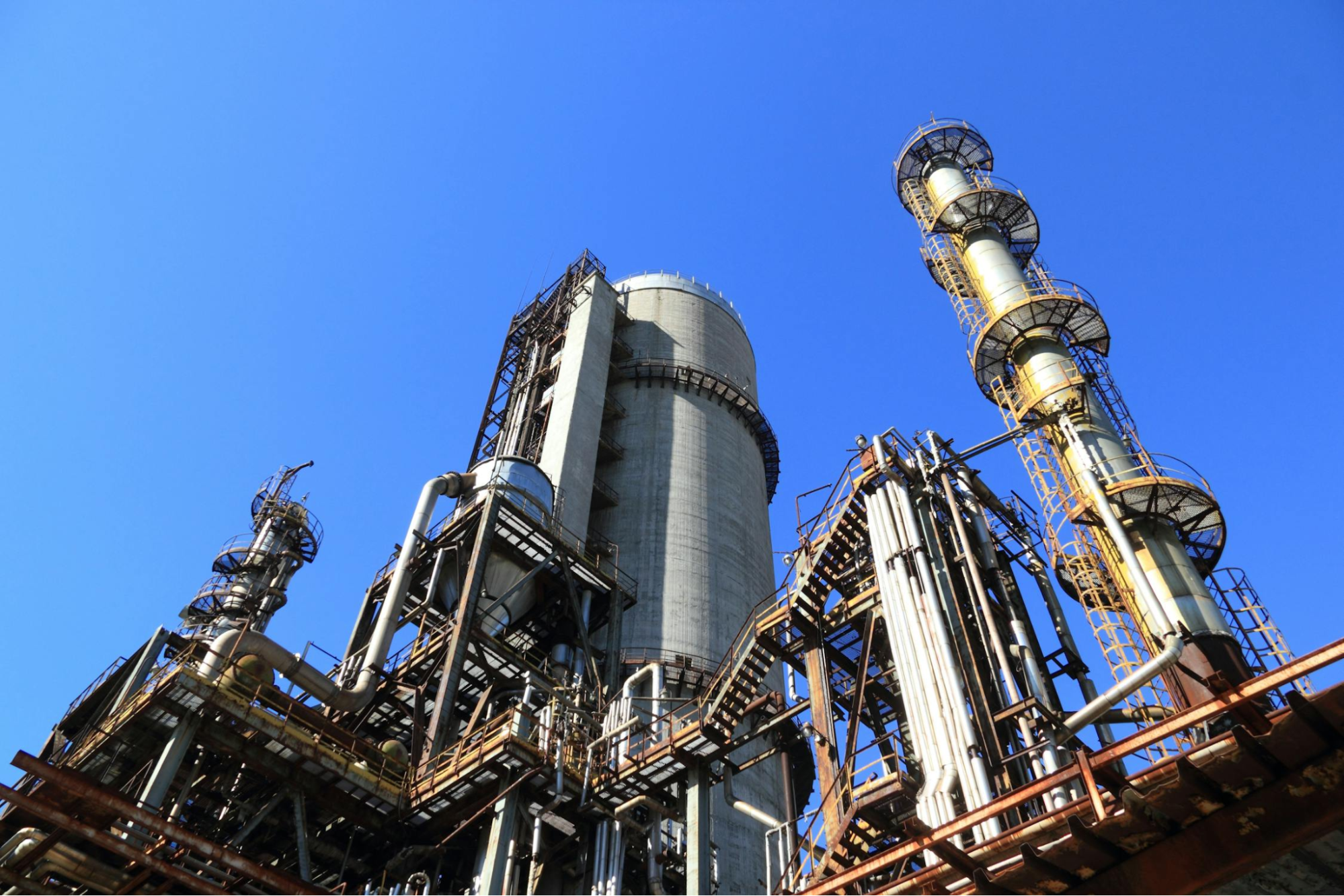
Consistent inspections, comprehensive documentation, and process audits can contribute to increased reliability of your production. Utilizing software solutions for tracking quality metrics provides valuable insights that help streamline operations and address issues before they arise. This emphasis on quality will not only enhance your brand’s reputation but will also foster customer loyalty as you consistently deliver high-caliber products.
Building Strategic Partnerships
Forming strategic partnerships is crucial to expanding your manufacturing capabilities. Collaborating with other manufacturers or service providers can complement your operations, enhance resource sharing, and amplify your market reach. Networking with industry professionals at trade shows, workshops, and conferences can lead to valuable connections that could be beneficial for collaborative projects. Consider partnering with technology firms specializing in the latest manufacturing innovations. These strategic alliances can benefit your production processes by equipping your facility with cutting-edge tools and methodologies. Enhanced collaboration across all facets of manufacturing not only broadens capabilities but also ensures that scalability efforts remain adaptable to changing market trends, thus providing lasting success in a competitive environment.
Embracing Sustainability
Sustainability has emerged as a non-negotiable aspect of modern manufacturing. Today’s consumers and businesses alike favor companies that prioritize environmentally friendly practices. By implementing sustainable manufacturing solutions, companies can significantly contribute to preserving resources while reducing waste. Utilizing recycled materials, optimizing energy consumption, and minimizing emissions are essential components of a sustainable approach. Adopting practices that focus on reducing carbon footprints can also lead to cost savings and improved efficiencies in production.
Showcasing your commitment to sustainability can differentiate your business in a crowded marketplace. As you develop scalable manufacturing solutions for metal components, consider how these practices can be integrated into your operations, thereby establishing your brand as a responsible leader in the industry. Being attuned to the evolving demands of consumers ensures long-term viability and market relevance.
Finding scalable manufacturing solutions for metal components requires a comprehensive approach, from understanding your production needs to incorporating the latest technologies, materials, and quality control practices. By focusing on automation, strategic partnerships, and sustainability, manufacturers can position themselves for growth and adaptability in an ever-changing market. Embracing these strategies ensures the long-term success and competitiveness of your operations.